Effective ways for work order management
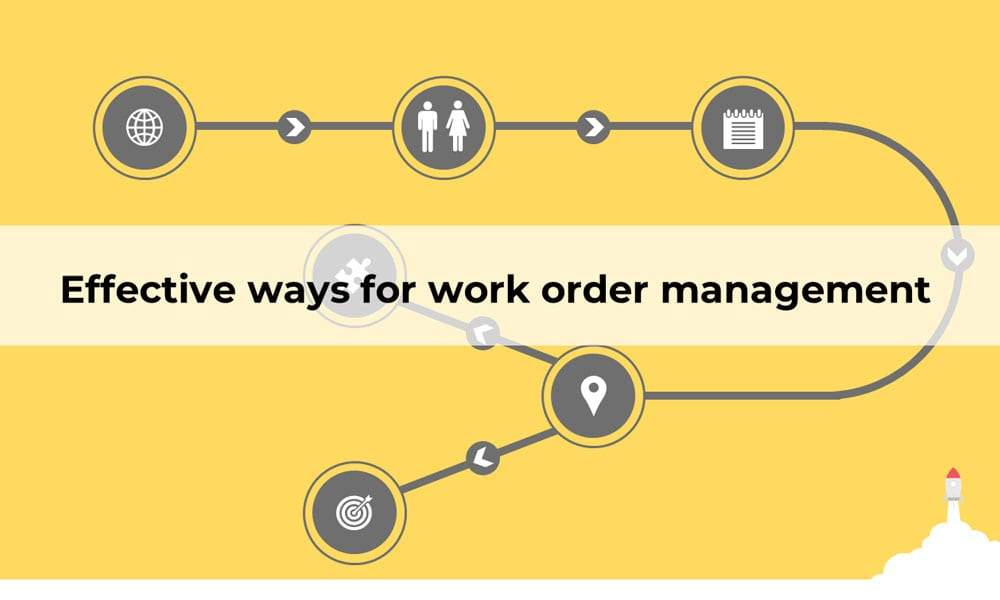
What is work order management?
A work order is a task or a job that is carried out to fix a problem. Previously, tasks or jobs were performed manually where an employee created a work order to fix the problem. Though there was nothing wrong in this process over a period of time, manual job gets a little difficult to manage. As it becomes challenging to track the progress of the work and its expenditures. It also becomes difficult in tracking the history of work completed.
During the past three decades, the company’s operations management has greatly evolved. Fluctuating economic conditions, increased market place competition and a move toward computer technology are largely responsible for companies across all sectors adopting a “smarter” operations approach. Today there are many maintenance software available. Depending upon the organization, the nature and cause of the work may change.
For example:
A service management organization may use work order to manage the services performed/carried for a customer.
A production organization uses work order for maintaining the assets which are important in increasing the asset availability.
A fleet management enterprise will use work order to track the vehicles and their breakdown
The following are 5 tips to efficient work order: –
1. Turn each request into Work order: –
Normally for scheduled jobs, system creates work order automatically. But for Corrective maintenance or sudden breakdowns work order needs to be created manually. It is very important to create a work order for every request. Even a new project that was discussed during the meeting or through email should be converted into a formal request. This is vital for analysis at year-end for budgeting the next financial year.
2. Prioritize & Schedule all requests: –
All requests need to be prioritized so the urgent request can be fixed first. In Effective Asset Management (EAM), Assets are crucial and all the parameters like location, safety, spare parts, and priority, etc are defined. When a work order is created on these assets, priority of the work order is taken in. Based on the industry, the deadline for each priority is defined. The schedule is done based on priority and to plan the resources, spare parts, and tools to achieve the deadline. The schedule is usually prepared by a maintenance planner.
3. Use of mobility: –
One of the key improvements in Effective Asset Management (EAM) is the use of mobility. Using mobility data helps in being maintained uptodate. Mobile devices are mainly used by technicians who carry work in harsh environments and remote areas, but the information like the inspection details that are observed or corrected are vital for the Asset. Also, a mobile app is very easy to use and handy while the work is being carried at such places, as most of the mobile solutions work both online and offline. Use of mobile reduces the duration of work as shown below.
4. Applying Failure code to Request: –
Increasing Asset availability is key in any Effective Asset Management (EAM). This is achieved by maintaining the Failure Code hierarchy. All assets must be tagged with failure hierarchy i.e., Problem, Cause, and Remedy. In a work order request mainly for Corrective maintenance Failure code is made mandatory while closing. This leads to creating new codes when failure is not maintained, or new failure is observed. This data can be analyzed, and action can be taken to overcome the failures.
5. Process work orders using workflow: –
All organizations have a process to execute the request. These processes involve several individuals and other departments. Using predefined workflow, request are automatically assigned to the available resource and keeps track of the time and escalates if time-bound is breached. Relevant people get timely notifications.
Work Order Management is increasingly becoming a necessity as the nature of work expands. Optimize MRO helps its clients to manage their work orders in the most systematic way by using new technology and trying their best to cause minimum error. The experts here make sure to reduce human labor and still make sure to deliver the best results.